Integrating machine learning, optimization and simulation to increase equipment utilization: Use case study on open pit mines
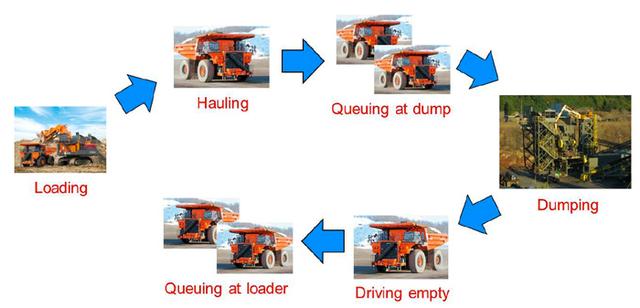
In mining operations, huge quantities of ore and waste material at mine sites are transported using extremely large equipment 24 hours a day. Material transportation represents up to 50% of operating costs in open pit mining [1]. In order for mining companies to have sustainable and economical mining operations, they must do two things: (i) Constantly improve what is known as overall equipment effectiveness (OEE) for their field equipment (ii) Reduce operating costs. In the last decade, the focus has been on operating cost reduction, and it has been mainly achieved by increasing the capacities of the equipment. Nowadays, with limited budgets the focus is on improving OEE, where due to huge equipment operational costs, even small gain in operational efficiency can result in savings of 10s-100s million dollars depending on the mine size. Improvement in OEE can be primarily achieved by two means: (i) increase availability of equipment (ii) increase utilization of available equipment. We focus on the latter problem, i.e., increasing equipment utilization by better planning and optimal management of the equipment.