寸法精度の2倍向上と不純物量の30%低減を実証
日立は、複雑な形状の部品を高精度・高品質に製造することができる金属3Dプリンター向け積層造形プロセス技術を開発しました。本技術は3Dプリンターの機種や使用する材料の種類に応じて最適な造形設計を行う設計システムにより、手動設計と比較して製造部品の寸法精度を2倍以上向上することが可能です。また、新たに真空・予熱機構を設置した金属3Dプリンターにより、従来装置と比較して、不純物の含有量を30%低減できることを実証しました。
今後、日立は、さまざまなパートナーと連携して開発技術の実用検証などを推進し、金属積層造形による革新的なモノづくりの実現に貢献します。
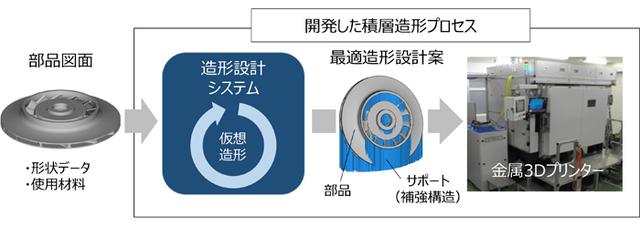
図1 開発技術を用いた金属積層造形の例
背景および取り組んだ課題
- 近年導入が進んでいる金属3Dプリンターによる積層造形においては、設計者の負担を軽減するデジタル技術を用いた造形プロセスによる高精度化、高品質化が求められている
- 製造部品の高精度化を実現する設計システム、製造部品の高品質化を実現する3Dプリンター機構の最適化が必要
開発した技術
- 仮想造形を繰り返すことで最適な造形設計案を提供する金属積層造形設計システム
- 不純物混入や製造部品の割れを抑制する真空・予熱機構を有する4レーザービーム金属3Dプリンター
確認した効果
- 変形評価用の試験片の造形案を設計した結果、従来の手動設計と比較して製造部品の寸法精度を2倍向上できることを確認
- 従来装置と比較して、不純物量を約30%低減、工具鋼系部品において、割れが発生しないことを確認
発表する論文、学会、イベントなど
- 本発表の一部は、2019年9月25~27日に東北大学で開催された日本機械学会第29回設計工学・システム部門講演会で発表済
開発技術の詳細
1. 最適な造形設計案を提供する金属積層造形設計システム
金属3Dプリンターを利用して部品を積層造形する際、造形中の変形を防ぐため、サポートと呼ばれる一時的な補強構造を加え、造形後にサポートを除去します。しかし、製造部品の形状が複雑になるにつれて、サポートの設計も困難となり、設計者が手動で設計する必要がありました。今回開発したシステムでは、利用する金属3Dプリンターの機種や材料の種類に応じて、造形シミュレータを活用して仮想空間での造形を繰り返すことで、最適な造形設計を提案します。具体的には形状データと材料の物性データおよび造形条件データを用いて造形シミュレーションを行い、サポート配置面に発生する力の分布を計算して、力の強弱に対応したサポートを設計します(図2)。これにより、手動設計と比較して、部品の寸法精度を約2倍に向上するとともに、サポートの体積を約4割低減することが可能です。
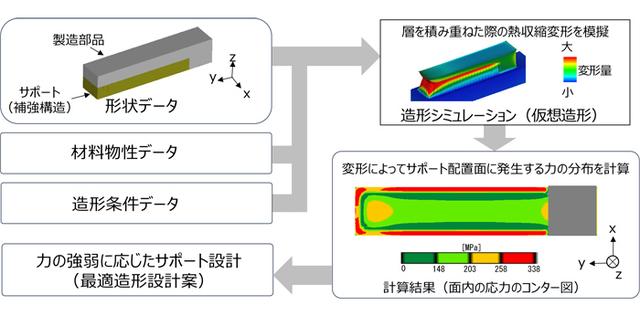
図2 開発した造形シミュレータを用いた造形設計システム
2. 真空・予熱機構を有する4レーザービームの金属3Dプリンター
金属3Dプリンターに真空機構を設置したことにより、造形する部品の周りから酸素を含む空気を排出することを可能としました。これにより、酸化物などの不純物混入の少ない高純度な部品の造形ができるようになり、従来装置と比較して不純物濃度を約30%低減しました。また、造形中の部品の温度を予熱機構で制御することにより、工具鋼系部品において、割れが発生しないことを確認しました。さらに、4レーザービームの同時使用により1ビーム使用時と比べて2倍以上の高速造形を実現しました。
照会先
株式会社日立製作所 研究開発グループ
問い合わせフォームへ